WHAT are the advantages of laser welding?
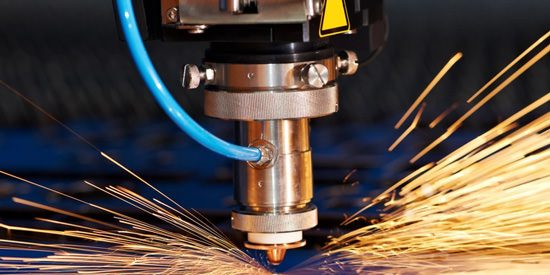
When compared to alternative welding methods, using lasers for welding offers certain clear advantages. Many of these benefits are connected to the capability of laser welding to produce a “keyhole.” This keyhole allows heat to enter not just at the top surface but also through the material’s thickness (s). The following list outlines the key benefits of this:
Swiftness and adaptability
A particularly quick method is laser welding. Thin-section materials can be welded at rates of several meters per minute, depending on the kind and power of the laser being utilized.
Therefore, lasers are perfect for use in highly automated situations with great productivity. Productivity advantages are also possible for thicker sections since the laser keyhole welding procedure may finish a connection in a single pass when conventional methods would need many passes.
The optical fiber supplied beams from Nd: YAG, diode, fiber, and disc lasers, in particular, can readily be remotely adjusted utilizing multi-axis robotic delivery systems, resulting in a geometrically flexible production process. Laser welding is almost usually carried out as an automated process using a laser welding machine.
Narrow, deep welds
High aspect ratio welds may be produced using laser welding (large depth to narrow width). Therefore, laser welding is an option for joint designs where many conventional (conduction constrained) welding processes are inappropriate, such as stake welding through lap joints. As a result, flanges may be employed in smaller sizes than with parts created with resistance spot welding.
Low heat input and distortion
A keyhole may be made using the extremely focused heat produced by lasers. As a result, samples welded with laser welding deform less than those welded with many other procedures since the amount of weld metal produced is little and only a tiny amount of heat is transmitted into the surrounding material. The short width of the heat impacted zones on each side of the weld, which results in reduced thermal damage and property loss in the parent material next to the weld, is another benefit of the low heat input.
Steels, stainless steels, Al, Ti, and Ni alloys, plastics, fabrics, and many other materials, both metallic and non-metallic, may all be connected or welded using lasers. In addition, depending on the kind and power of the laser being utilized, the thickness of the material that can be welded can range from less than a millimeter to over 30mm.
Carried performed without a vacuum
Laser welding is done at atmospheric pressure, in contrast to the bulk of electron beam keyhole welding procedures, however, gas shielding is frequently required to stop the welds from oxidizing.
Single-sided, non-contact procedure
In most cases, laser welding is a single-sided process—that is, it completes the union from only one side of the workpieces—and it does not apply any force to the components being connected. Weld root shielding, on the other hand, may be necessary from the opposing side, as is the case with many other fusion processes.
Intermittent welding
If necessary, spot or stitch welds may be produced with lasers just as quickly as continuous welds.
Versatility
Aside from welding, a laser source may be used for a variety of other material processing tasks, such as cutting, surface, heat treating, and marking, as well as more complicated processes like rapid prototyping. Additionally, other approaches may be taken to the delivery of the beam(s) to the workpieces, including:
One laser source may handle several operations by sharing a single beam across various welding stations. One laser source may process two distinct areas on a workpiece (or the same area from opposite sides) by sharing the energy of a single beam.
Using specialized transmission or focusing optics, beams may be divided or shaped to treat materials with a variety of energy distributions.